Model NO.: SJ100
Customized: Customized
Certification: CE, SGS
Condition: Used
Capacity: 100-500kg/H
Screw and Barrel: 38CrMoAl, Nitrogen, Bimetallic
Application: PVC
Degassing: One Vacuum
Pelletizing Way: Wind Cooling Hot Die Faced
Delivery Time: 45 Working Days
Extruder: Single Screw Extruder
Cooling Way: by Wind
Heater: Cost Al or Cost Copper
Ld: 28:1
Trademark: JORBIN
Transport Package: Film Packing and Wood Base or Wood Case
Specification: pellets size Φ 2.5*3mm
Origin: Zhangjiagang City
HS Code: 84772010
Model NO.: SJ100
Customized: Customized
Certification: CE, SGS
Condition: Used
Capacity: 100-500kg/H
Screw and Barrel: 38CrMoAl, Nitrogen, Bimetallic
Application: PVC
Degassing: One Vacuum
Pelletizing Way: Wind Cooling Hot Die Faced
Delivery Time: 45 Working Days
Extruder: Single Screw Extruder
Cooling Way: by Wind
Heater: Cost Al or Cost Copper
Ld: 28:1
Trademark: JORBIN
Transport Package: Film Packing and Wood Base or Wood Case
Specification: pellets size Φ 2.5*3mm
Origin: Zhangjiagang City
HS Code: 84772010
Â
PVC Granules  single screw extrusion machine, blending and modification, functional parent granule(black carbon granule, flame-retardant granule, degradable granule, double protective granule), various cable, special material(EVA, flurin rubber, TPR sole material, UV protection material), reactive and extruding, powder coating.
Working Principle
First by the high speed mixer, you can mix all material equally accroding to its different percentage. Then we send the mixing material into hopper by screw charger, our hopper is special desinged, so the material in the hopper won't getogether. Different material with different screw design to meeting the feature of material.Â
The advantages of this machine
1. Highly efficent: the machine is automatic and with less power consumption.
2. Special screw design: We will design the screw up to customer different material and the material of screw and barrel can be 38CrMoAL or bimetallic.
3. High capacity: the capacity of the machine is about 80kg/h, we can do the machine up to 1000kg/h
5. The machine wih long life.
Line components
Item NO. |
Item name |
Quantity |
Power |
1 |
SJ100/28 Single screw extruder |
1set |
55kW |
2 |
Three Feeders |
1 set |
1.5 |
3 |
Hot cutter mould |
1set |
-- |
4 |
Wind-cooling rubs surface hot cutter |
1set |
1.1kW |
5 |
The first wind transmission system |
1set |
3kW |
6 |
cyclone separator |
1set |
-- |
7 |
Wind-cooling vibrator |
1set |
0.8+1.2kW |
8 |
The second wind transmission system |
1set |
3kW |
9 |
Silo |
1set |
-- |
10 |
Electric control cabinet |
1set |
-- |
More machine photoes
Feeder and main machine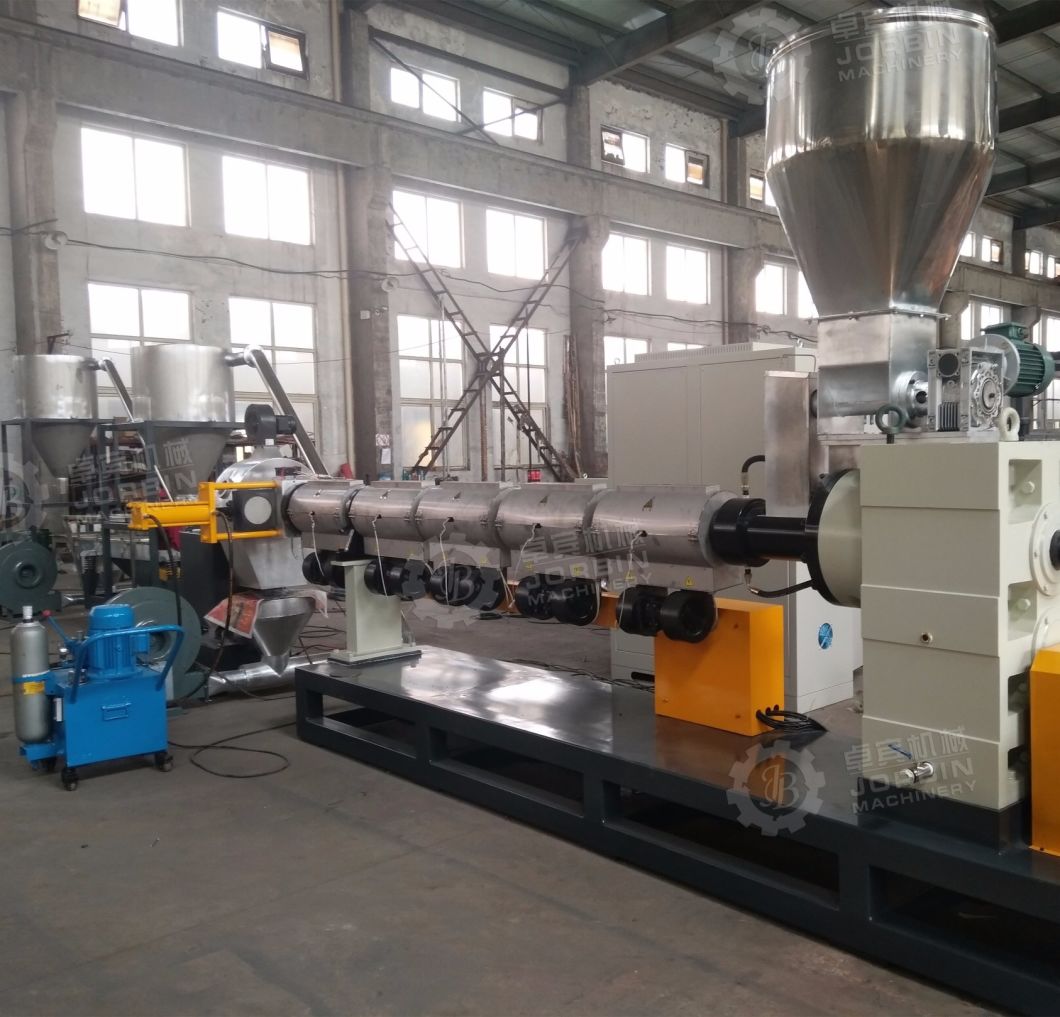
Machine line
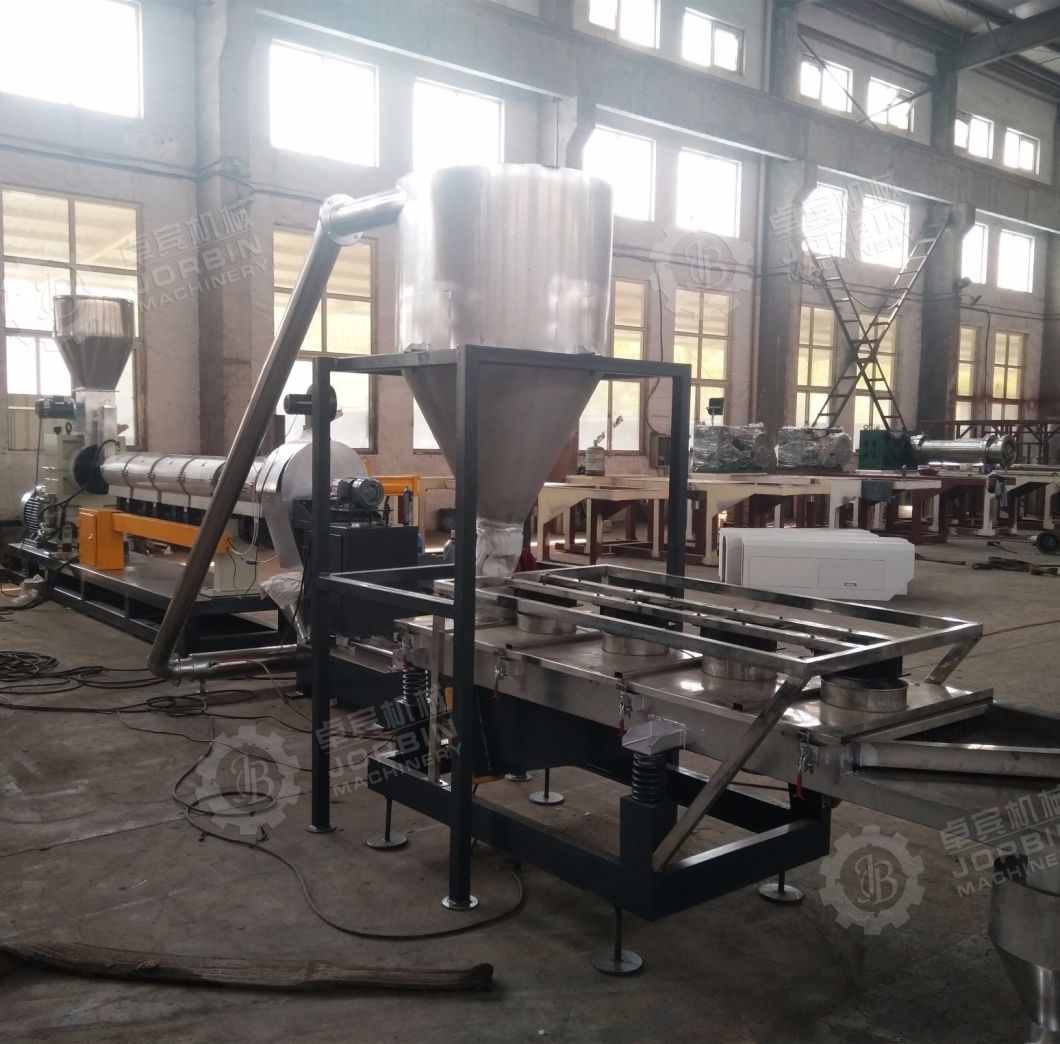
Die of the machine(With wind cooling pelletizing way)
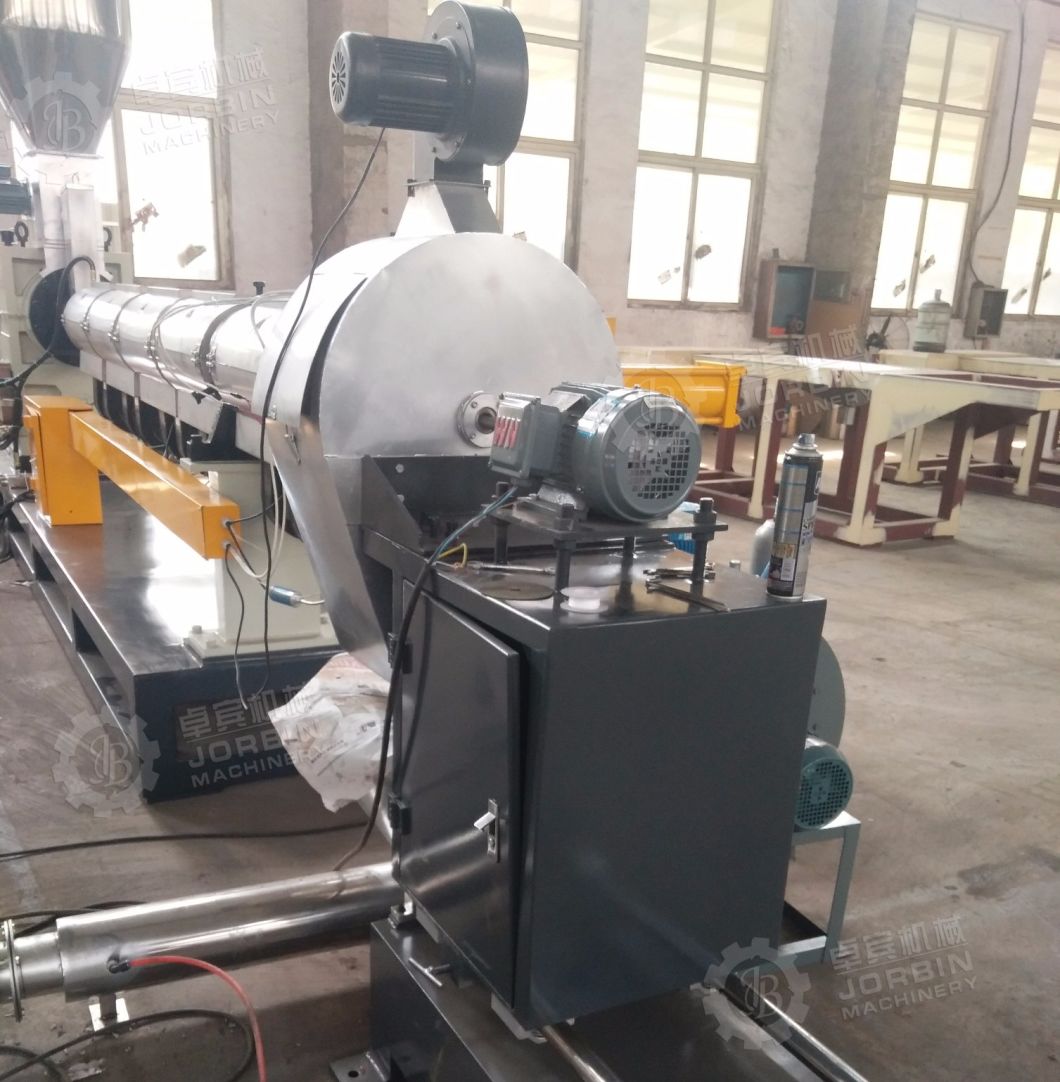
Wind cooilng vibration
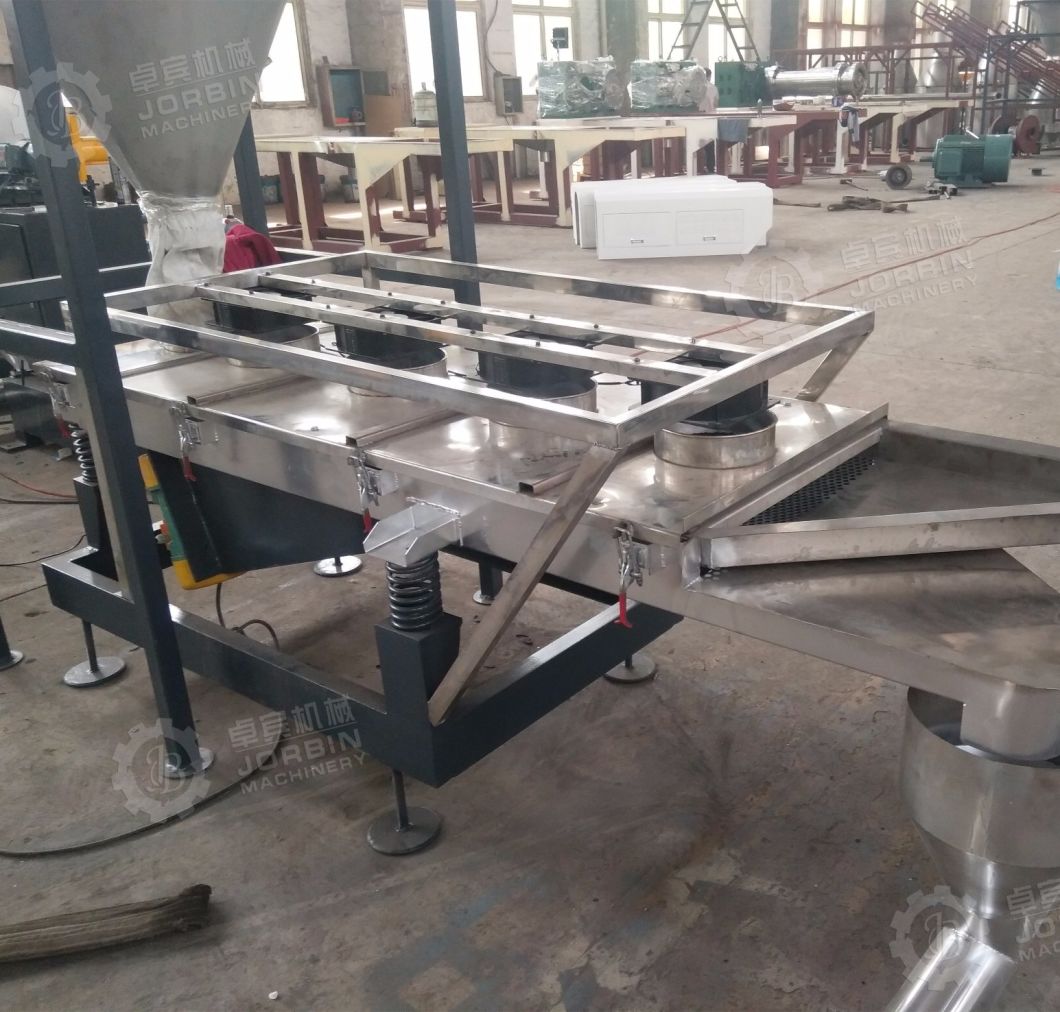
Two step wind transmission system
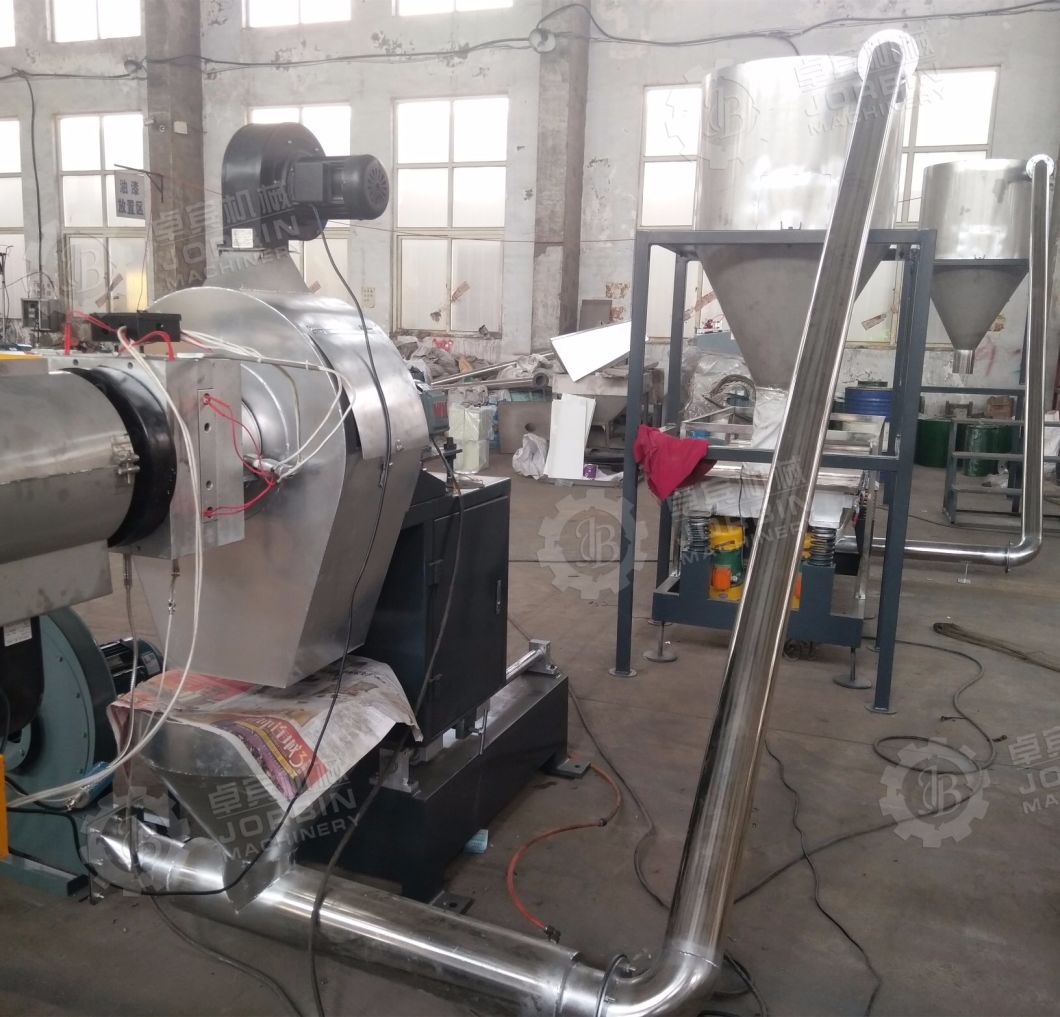
If you need  more details of this kind of machine kindly contact me, I can send you more detail photoes and  vedios.

1. We supply below necessary documents with the machine:
- Machine layout
- Electricity diagram
- Machine certificate
- General manual book/maintenance book
2. We provides one-year quality guarantee. During this period, if the machine's malfunction is approved to be our responsibility, we will send the broken spare parts to you with DHL courier or other way within 7 workdays after receiving the complainant. And send the technicians to the buyer's factory for maintaining. All charges are in our account.
3. After one year guarantee, If you need we can provides payable spare parts and technician's VISITING maintenance, and any broken spares we can send you soon as possible.
4. We trust that our quotation meets with your requirements and we will gladly furnish you with further information.
5. 24Hours service :Â Â Cell+86-13915707468
                            Â
Â
PVC Granules  single screw extrusion machine, blending and modification, functional parent granule(black carbon granule, flame-retardant granule, degradable granule, double protective granule), various cable, special material(EVA, flurin rubber, TPR sole material, UV protection material), reactive and extruding, powder coating.
Working Principle
First by the high speed mixer, you can mix all material equally accroding to its different percentage. Then we send the mixing material into hopper by screw charger, our hopper is special desinged, so the material in the hopper won't getogether. Different material with different screw design to meeting the feature of material.Â
The advantages of this machine
1. Highly efficent: the machine is automatic and with less power consumption.
2. Special screw design: We will design the screw up to customer different material and the material of screw and barrel can be 38CrMoAL or bimetallic.
3. High capacity: the capacity of the machine is about 80kg/h, we can do the machine up to 1000kg/h
5. The machine wih long life.
Line components
Item NO. |
Item name |
Quantity |
Power |
1 |
SJ100/28 Single screw extruder |
1set |
55kW |
2 |
Three Feeders |
1 set |
1.5 |
3 |
Hot cutter mould |
1set |
-- |
4 |
Wind-cooling rubs surface hot cutter |
1set |
1.1kW |
5 |
The first wind transmission system |
1set |
3kW |
6 |
cyclone separator |
1set |
-- |
7 |
Wind-cooling vibrator |
1set |
0.8+1.2kW |
8 |
The second wind transmission system |
1set |
3kW |
9 |
Silo |
1set |
-- |
10 |
Electric control cabinet |
1set |
-- |
More machine photoes
Feeder and main machine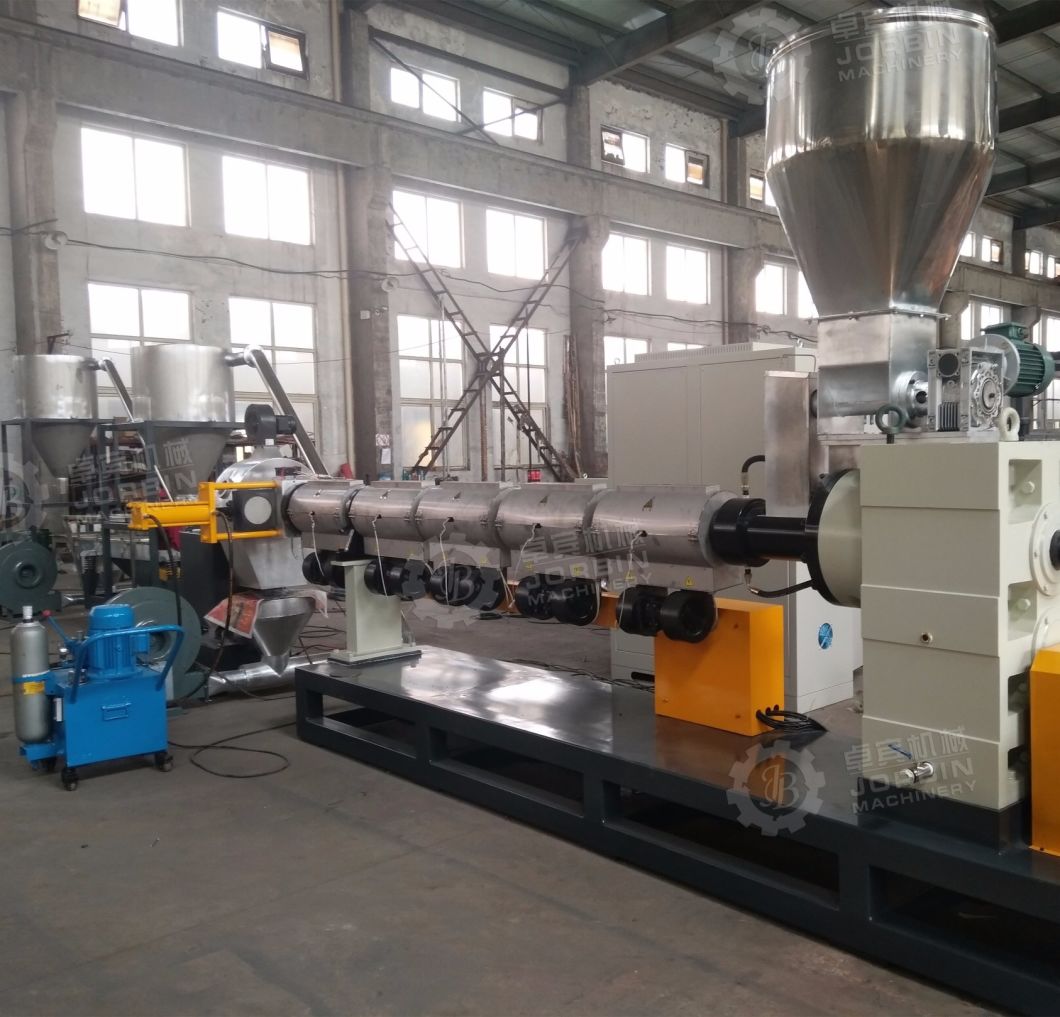
Machine line
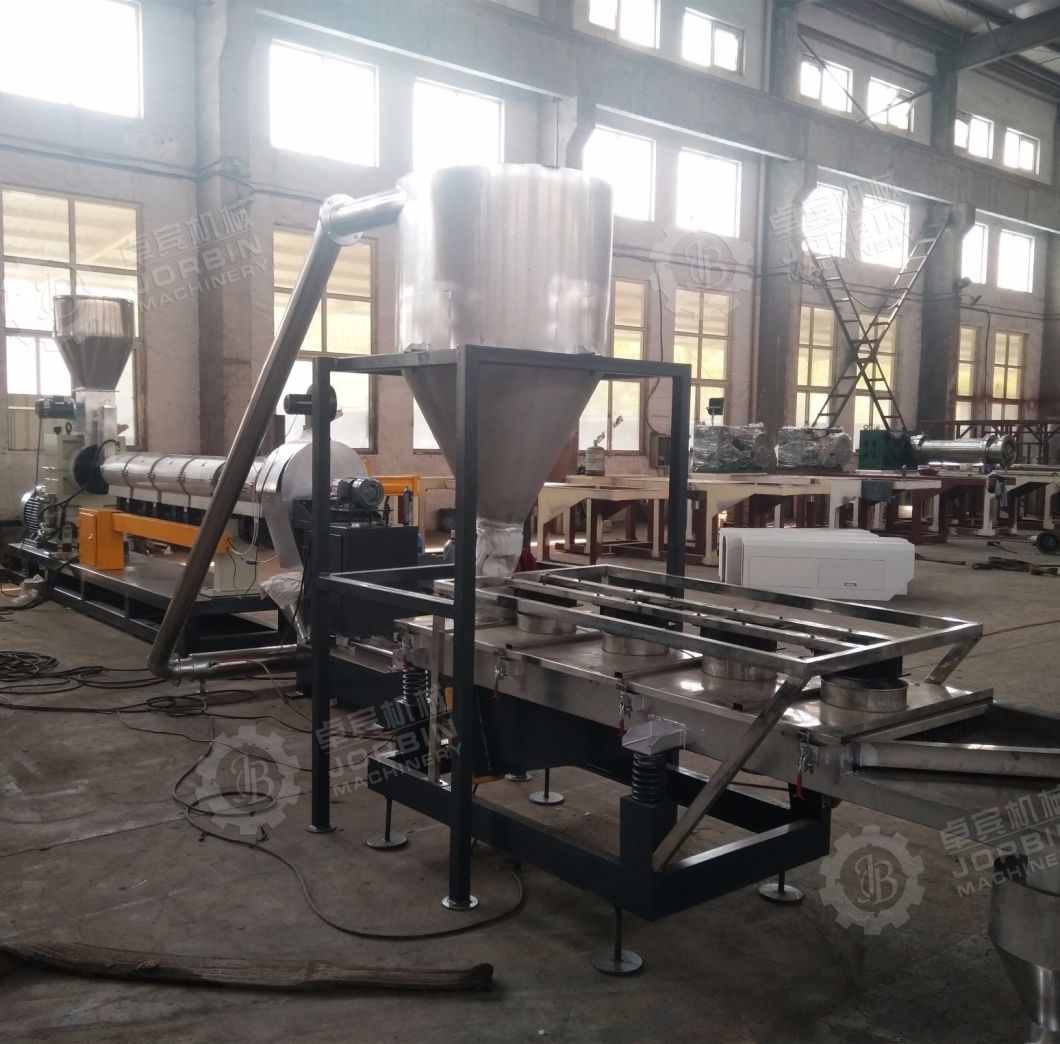
Die of the machine(With wind cooling pelletizing way)
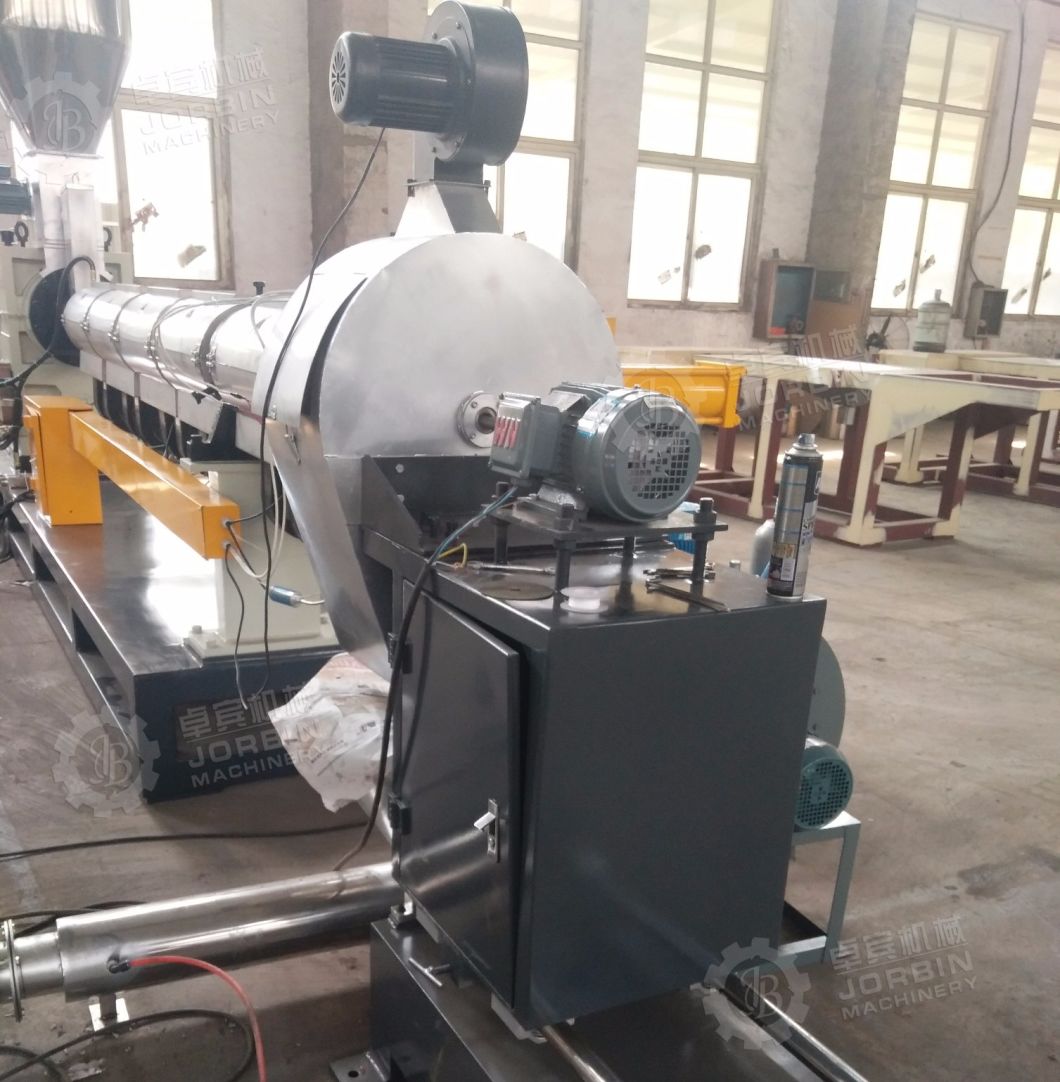
Wind cooilng vibration
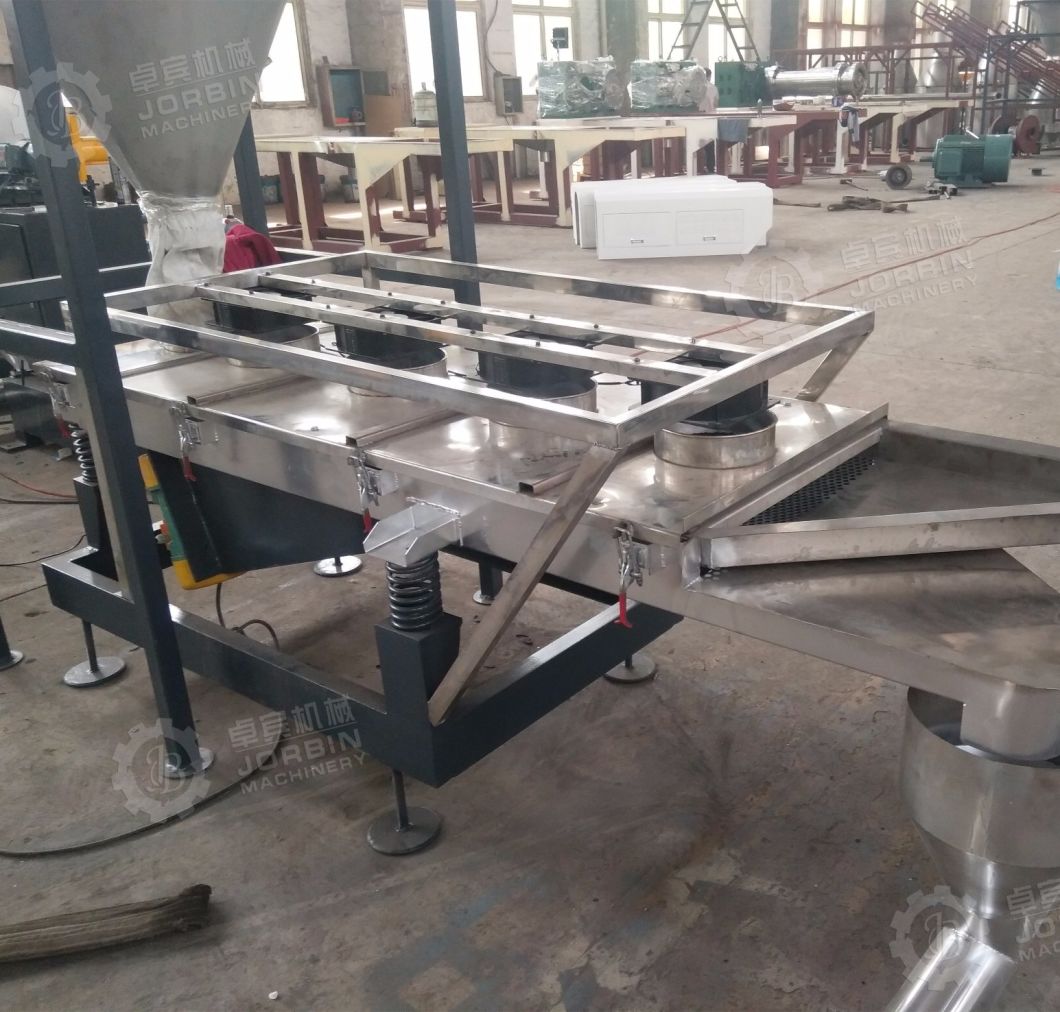
Two step wind transmission system
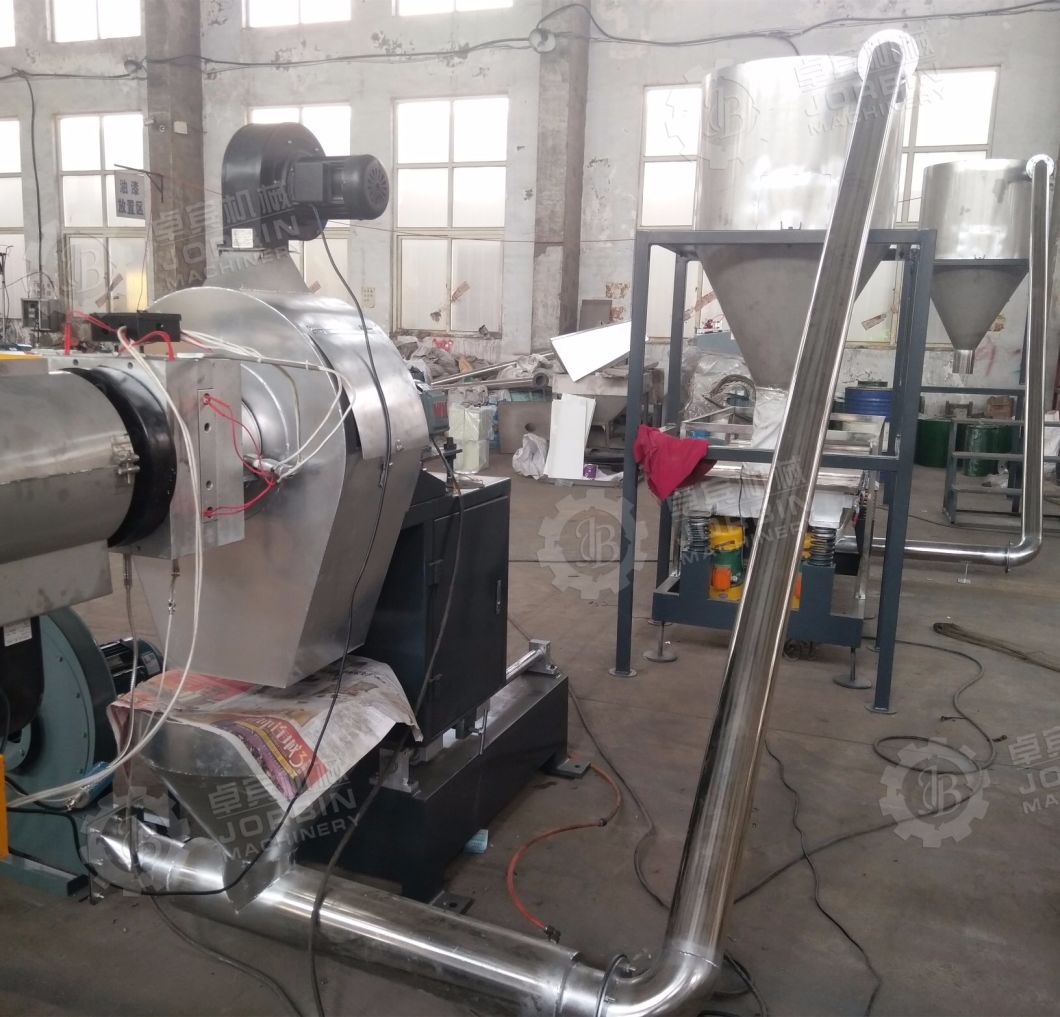
If you need  more details of this kind of machine kindly contact me, I can send you more detail photoes and  vedios.

1. We supply below necessary documents with the machine:
- Machine layout
- Electricity diagram
- Machine certificate
- General manual book/maintenance book
2. We provides one-year quality guarantee. During this period, if the machine's malfunction is approved to be our responsibility, we will send the broken spare parts to you with DHL courier or other way within 7 workdays after receiving the complainant. And send the technicians to the buyer's factory for maintaining. All charges are in our account.
3. After one year guarantee, If you need we can provides payable spare parts and technician's VISITING maintenance, and any broken spares we can send you soon as possible.
4. We trust that our quotation meets with your requirements and we will gladly furnish you with further information.
5. 24Hours service :Â Â Cell+86-13915707468
                            Â
Forging can produce a piece that is stronger than an equivalent cast or machined part. As the metal is shaped during the forging process, its internal grain deforms to follow the general shape of the part. As a result, the grain is continuous throughout the part, giving rise to a piece with improved strength characteristics. Additionally, forgings can target a lower total cost when compared to a casting or fabrication. When you consider all the costs that are involved in a product`s lifecycle from procurement to lead time to rework, then factor in the costs of scrap, downtime and further quality issues, the long-term benefits of forgings can outweigh the short-term cost-savings that castings or fabrications might offer.
Forging
|
MAIN PARTICULARS
|
Material for product
|
Aluminum
|
Standard
|
ASTM, ASME, DIN, JIS, ISO, BS, API, EN
|
Certificate
|
ISO9001, BV
|
Processing
|
Forging + blasting + Machining
|
Finishing surface
|
Machined surface with tectyl891, anodize, polishing, nickel plating, zinc plating and chrome plating, oxidation, powder coating, painting, etc.
|
Inspection
|
material, construction, dimension, heat treatment, hardness, NDT
|
Quality
|
ISO9001, BV,control production
|
The photos of our Aluminum Forging
Forging of aluminium
Aluminium forging is performed at a temperature range between 350 and 550 °C
Forging temperatures above 550 °C are too close to the solidus temperature of the alloys and lead in conjunction with varying effective strains to unfavorable workpiece surfaces and potentially to a partial melting as well as fold formation.
Forging temperatures below 350 °C reduce formability by increasing the yield stress, which can lead to unfilled dies, cracking at the workpiece surface and increased die forces
Due to the narrow temperature range and high thermal conductivity, aluminium forging can only be realized in a particular process window. To provide good forming conditions a homogeneous temperature distribution in the entire workpiece is necessary. Therefore, the control of the tool temperature has a major influence to the process. For example, by optimizing the preform geometries the local effective strains can be influenced to reduce local overheating for a more homogeneous temperature distribution
Application of aluminium forged parts
High-strength aluminium alloys have the tensile strength of medium strong steel alloys while providing significant weight advantages. Therefore, aluminium forged parts are mainly used in aerospace, automotive industry and many other fields of engineering especially in those fields, where highest safety standards against failure by abuse, by shock or vibratory stresses are needed. Such parts are for example chassis parts, steering components and brake parts. Commonly used alloys are AlSi1MgMn (EN AW-6082) and AlZnMgCu1,5 (EN AW-7075). About 80% of all aluminium forged parts are made of AlSi1MgMn. The high-strength alloy AlZnMgCu1,5 is mainly used for aerospace applications
Aluminum Forging
Aluminum Forging,Aluminum Forging Parts For Customization,Cnc Aluminum Forging,Aluminum Die Forging Part
UniSite Group , http://www.unisitemachining.com